America’s home builders are getting squeezed by the war in Ukraine. Here’s how
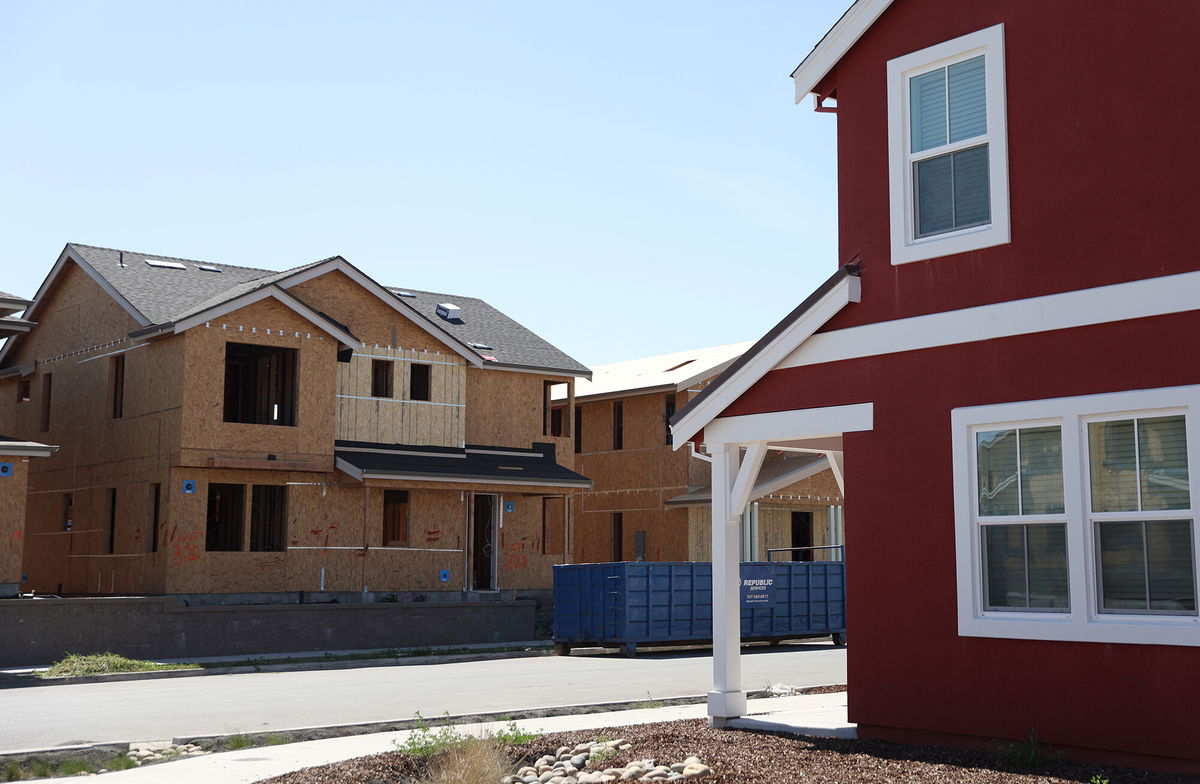
A home under construction stands across from a completed home at a housing development on March 23 in Petaluma
By Alicia Wallace, CNN Business
For the past few years, developer and home builder Estridge Homes could bank on the price quotes it received for asphalt holding steady for at least nine months.
That window is now 15 days.
For many home builders, supply chain disruptions from the pandemic have meant garage doors are on back order, floor tiles keep getting discontinued mid-construction, and appliances are marooned aboard waylaid shipping vessels.
Now, the Russia-Ukraine conflict is hitting commodities such as oil and metals, leaving US home builders to brace for further cost hikes and delays and putting the squeeze on already tight housing inventory and affordability.
“I do think the impacts are going to hit pretty quickly for the housing market,” said Scott Anderson, chief economist at Bank of the West. “We expect these things to get worse before they get better.”
Anderson and Bank of the West economists recently lowered expectations that housing starts — as the industry terms the construction of new homes — would pick up this year. They previously thought supply chain shortages and material price pressures would begin to ease. “But it doesn’t look like we’re going to see much of that — at least near-term here,” Anderson said.
Most of the materials and commodities the construction industry depends upon are seeing double-digit year-over-year cost increases, with steel and diesel seeing some of the largest gains, at nearly 75% and nearly 58%, respectively, according to the Associated General Contractors of America’s analysis of February Producer Price Index data.
“Even though the February numbers represent some of the highest year-over-year price increases ever recorded, they have already been surpassed by even steeper price hikes since the war in Ukraine broke out,” Ken Simonson, the association’s chief economist, said in a statement.
Adapting in a changing market
The past two years have been both good and bad for Indianapolis-based Estridge Homes, which specializes in building semi-custom homes that sell in the range of $500,000 to $1.5 million.
The nature of the pandemic and the rise of remote work resulted in some people fleeing the cities and settling into single-family homes in the suburbs or in other regions of the country. Estridge Homes witnessed an uptick in its out-of-state buyers from places like California and Chicago, said Clint Mitchell, the company’s chief executive officer.
Previously, about 20% of Estridge’s buyers came from out of state. Last year, that figure rose to 30%, Mitchell said.
“The demand for housing really increased across all ages,” he said. “People were valuing the home more, choosing to spend more on the home, and wanting to customize it like we offer.”
But Estridge, like many other home builders, couldn’t construct them fast enough. The time it takes for Estridge to build a home has increased by three to four months as compared to two years ago, he said.
That’s because the upheaval in the labor market caused by the pandemic meant workers — already a tight commodity — were even harder to come by, and snarled supply chains meant that building materials grew scarcer and more costly.
Estridge has tried to adapt on the fly by having customers select different fixtures and finishes or by popping in a temporary appliance or fixture with plans to install a permanent replacement once one finally becomes available.
“We’re having to make changes in about every home we’re building,” Mitchell said.
Along the way, prices for materials have gone up by more than 20%, increases that Estridge has been able to pass along to the customer.
“At some point, affordability does become an issue,” he said. “We haven’t seen it yet, but we’re definitely paying attention to that.”
But in recent weeks, material prices have risen even more aggressively because of the volatility in prices for commodities such as oil, which neared $130 a barrel after Russia invaded Ukraine. Prices have fallen slightly in the weeks since, but remain highly reactive.
Higher oil and commodity costs spill over to myriad areas in the construction supply chain, and some effects are more immediate than others: Gasoline is needed to feed earth movers, haul supplies and transport workers to job sites; petroleum serves as a building block in critical materials, like asphalt, steel, glues, pipes and paints; and growing everyday expenses could further hamper people’s ability to spend.
“We’re trying to anticipate what it will be a couple months from now,” Mitchell said.
A ‘reset’ is needed
Builders are well aware of the heightened need for more affordable housing, but best laid plans have fallen by the wayside, said Ali Wolf, chief economist of Zonda, a housing market research and consulting firm.
“Building entry-level homes has never been harder and more costly,” she said.
Affordable home builders, like Trellis in Phoenix, are feeling the squeeze.
“Our struggle is always making sure that we can maintain affordability or maintain the ability to deliver a home that may cost $400,000 or $500,000 nowadays to a family that could only maybe have a purchasing power of $200,000 or $225,000,” said Glenn Karlson, director of real estate development at Trellis.
Trellis has tried to make up the difference for buyers, including applying federal low-income housing tax credits, developing higher-density housing projects and offering lease-to-own properties, said Joel McCabe, Trellis’ chief operating officer.
However, the state of the economy and the nature of the housing industry — especially in a sizzling-hot market like Phoenix, where home prices are up more than 32% since last year — are causing those gaps to grow even wider, he said.
“We don’t really get to enjoy a market going up, because our buyer is not going to be able to come to the table with more down payment,” Karlson said.
Many prospective home buyers are struggling to meet area median income (AMI) qualifications for certain affordable housing programs, he said.
“We’re basically asking our clients to put their lives on hold for 18 months: ‘Don’t go buy anything. Don’t go buy a new car. Don’t switch a job, because God forbid you go from 79% AMI to 83% AMI. And because if you do, everything we can do for you goes out the window, and now you don’t get to buy a house,'” Karlson said.
Knocking down costs hasn’t been an easy endeavor either. As a smaller nonprofit, Trellis doesn’t have the same economies of scale and buying power as the large commercial builders.
“We’re usually the last person in line to receive our product,” Karlson said.
So the company has turned scrappy, implementing a “rob Peter, pay Paul strategy” by allocating appliances and fixtures to the units and homes that are the closest to delivery, scouring secondhand warehouses for “scratch-and-dent” appliances that can make do in a pinch, or designing floor plans specific to what direction the house is facing to maximize energy efficiency and cost savings.
Despite the efforts, the delays and higher costs have been significant: Before the pandemic, it took about five months to build a house at a cost of $120 to $135 per square foot. Now it’s 18 months at a construction cost of $185 to $200 per square foot.
The shrinking affordability has sparked discussions in policymaker circles as to how to address these challenges, whether through expanding subsidies, creating inclusionary zoning, or requiring low- and mid-range housing in new developments in areas like downtown, McCabe said.
“Those conversations now are happening, so that is hopeful,” he said.
But policy takes time, and concerns are growing as to how unsustainable the current trajectory of the industry is, Karlson added.
“It’s going to get to a point where even the traditional everyday person will not be able to buy a home,” Karlson said. “The only way to make this change is there’s got to be a correction. I’m not saying a recession or a depression, but sometimes a reset is exactly what is needed.”
The-CNN-Wire
™ & © 2022 Cable News Network, Inc., a WarnerMedia Company. All rights reserved.